Assembly line for Thule
How the line is built
We had the pleasure of delivering an assembly line to Thule for assembling their Fixpoint, the foot for attaching roof racks to car roofs. The assembly line consists of five workstations: three robot-equipped "multicubes" for assembling components, with a pallet conveyor running through these three cubes, equipped with about 30 pallets with fixtures on which the foot is built. There is also a "multihandler" for robotic handling of large plastic parts, and a packing station with box erection and various control functions to ensure the product's quality.
In total, 10 different components are handled and assembled into a complete foot, packed in a box that is eventually delivered to Thule’s customer. The capacity is one complete box with four feet every 44 seconds, which equates to 11 seconds per foot.
In the first "multicube," a metal component is assembled, with parts being fed using our "vision feeders" to two robots that together mount these three components onto the fixture. In the second "multicube," two more parts are fed using our "vision feeders," which are then handled, pressed together, and placed into the fixture by a robot. Another three components are fed in and assembled using our special equipment and a robot. In the third "multicube," one of the components is riveted and inspected, and two large plastic components are picked and mounted onto the fixture by two robots, making the foot complete. Final marking is also performed at this stage. Four feet are placed in the final box, which then moves to the packing station.
In the "multihandler," a robot picks the two large plastic components from Thule’s boxes and places them on our material pallets. The pallets move on a conveyor, creating a buffer and supplying the third "multicube" with parts. In the packing station, a chain conveyor transports the final box from the automatic box erector into "multicube 3" and onward to the manual packing station, where the box is completed. The box is then sealed, weighed, and, once approved, transported further.
Our "multicubes" and "multihandler" are complete standalone units equipped with their own control systems, valve terminals, robot controllers, and operator panels. These units are then integrated into a full line with an overarching control system for optimal safety and availability.
40 years of experience with special machines
At Axelent Engineering, we have extensive experience in special machines, having delivered to a wide range of customers since our founding in 1972. In the field of special machines, solutions can range from complete automation systems to smaller subsystems, with each project being unique and customer-specific. New technologies and methods/processes have cross-fertilized through projects and industries, and we always take our customer’s specific conditions into account.
We thank Thule for the trust!
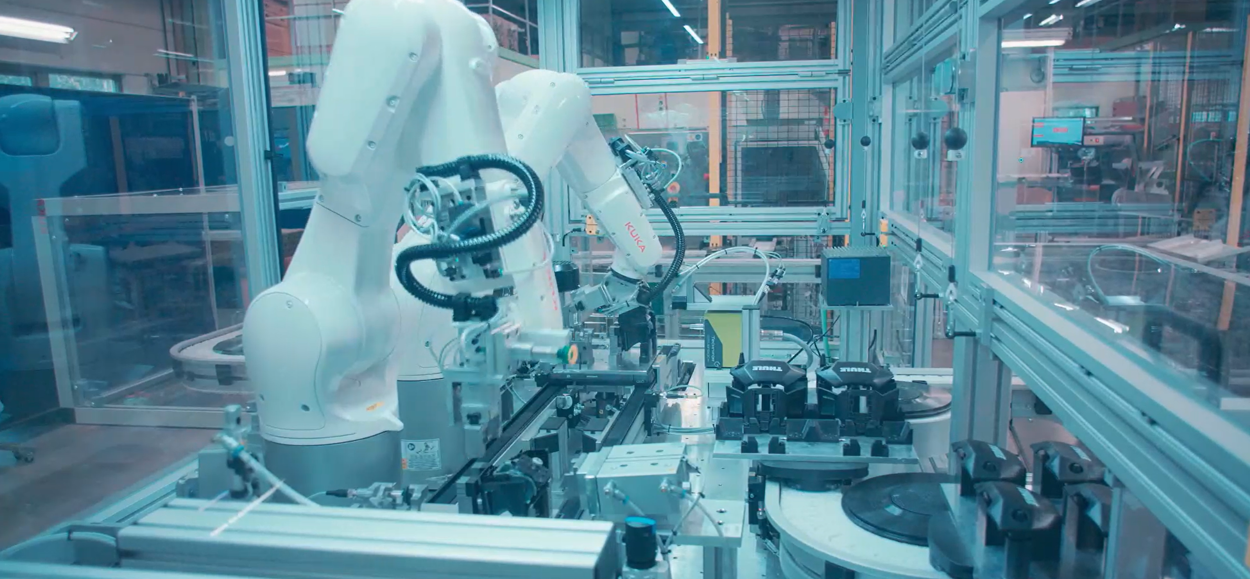
Services
Machinery & Automation
For us at Axelent Engineering, automation is about one thing: creating profitable workflows. This involves not only hardware but also software and work processes. Our focus on profitability, combined with over forty years of experience in designing and manufacturing special machines, has made us a leading knowledge company in Sweden.
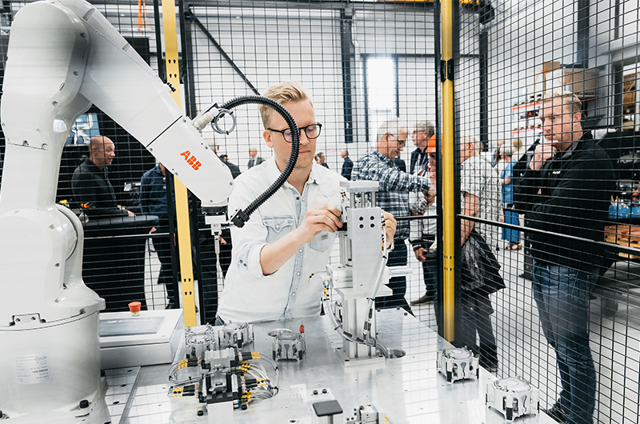
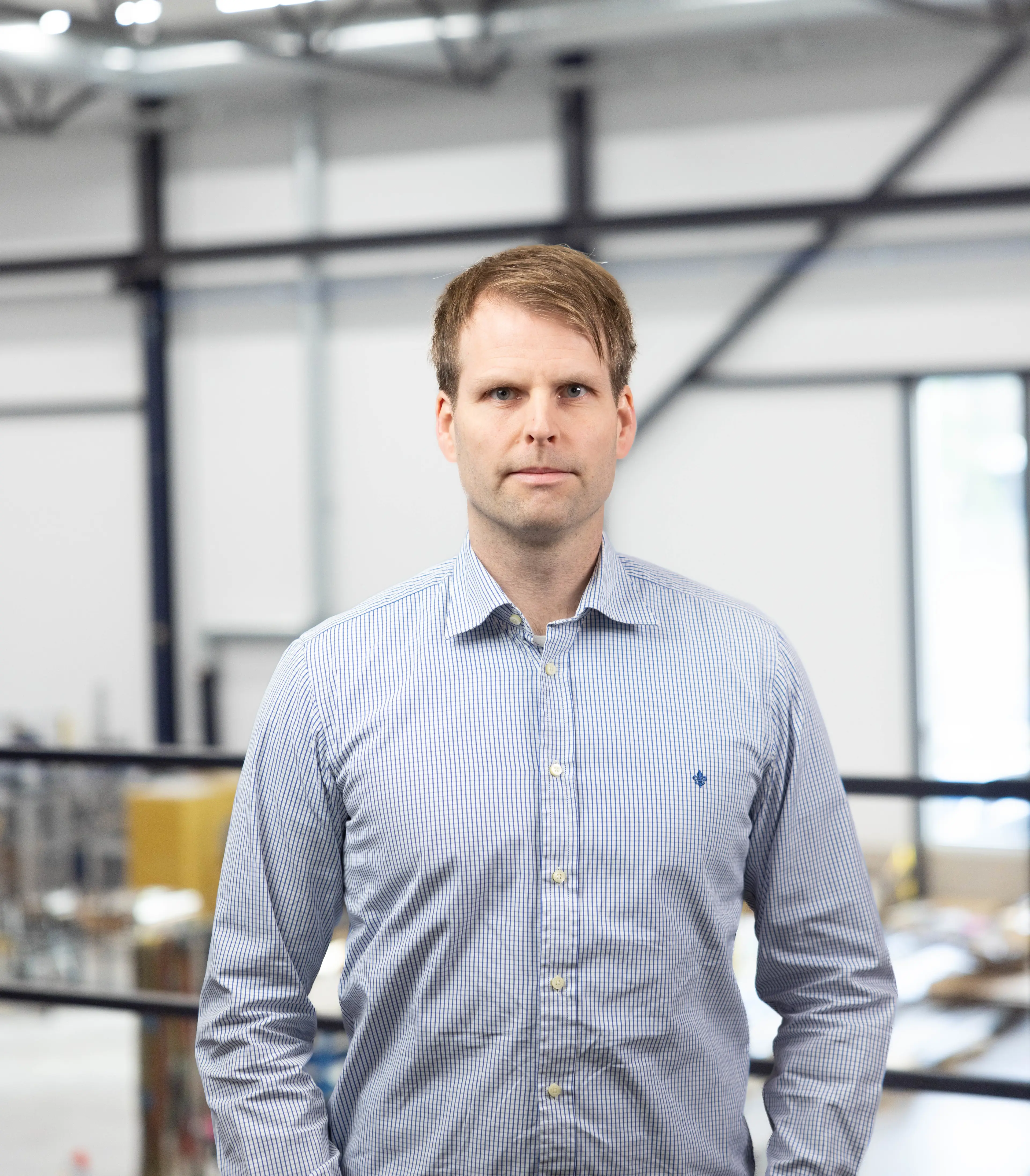
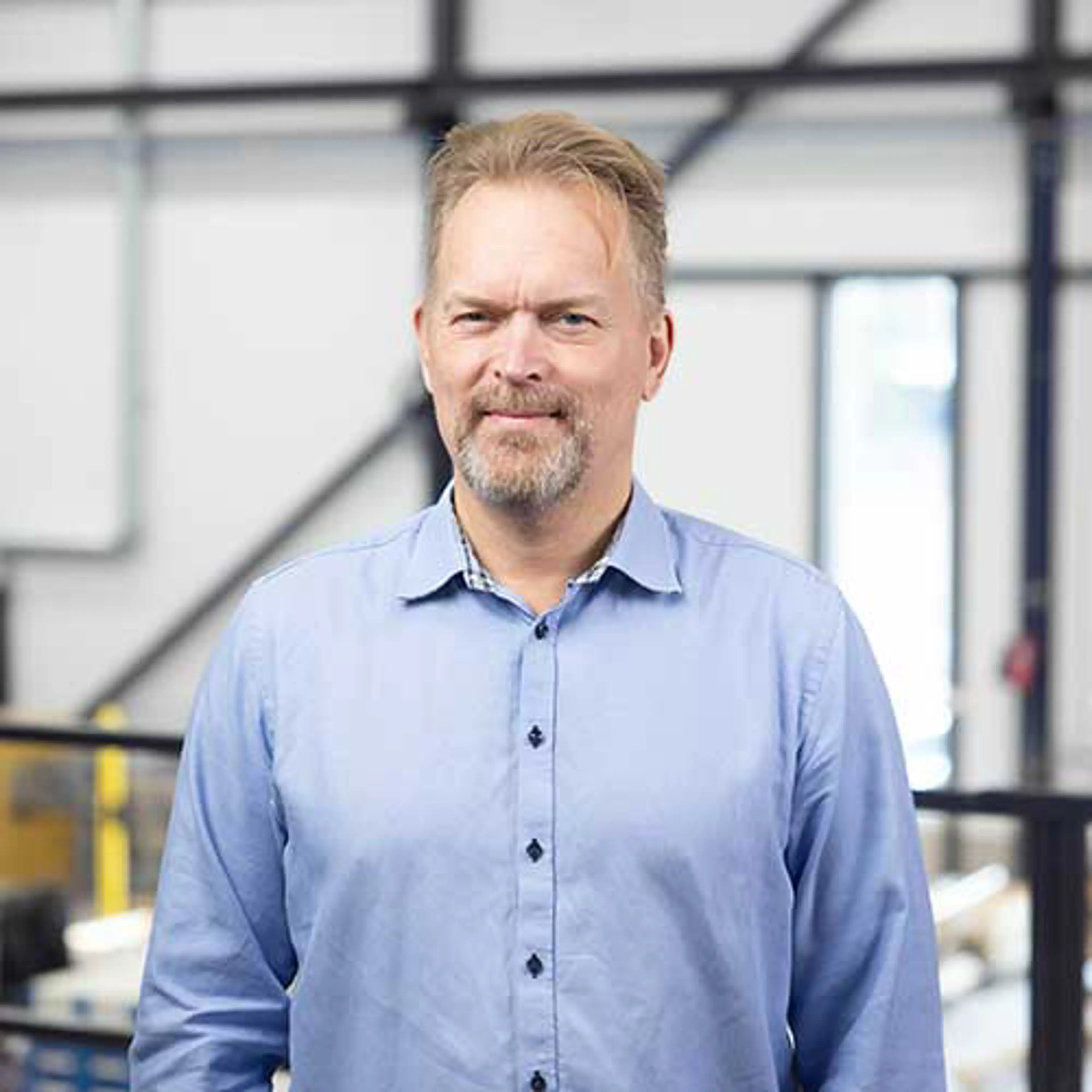
Frederik Sörensen